BOM Services
Home / Compliance Solutions / Component Engineering / BOM Services
BOM Validation
It is critical in a manufacturing process to ensure that their products are well-designed, well- manufactured, and meet regulatory standards. It also helps them determine if they will be able to meet their customers' expectations.
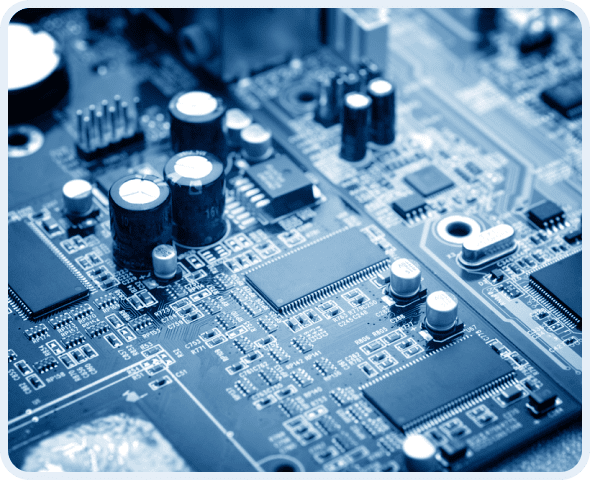
How do BOM Services work?
The BOM validation process starts with reviewing the design specifications and drawing sheets for the product, which includes all the components that are needed to assemble it. Once this step is completed, the BOM will be validated against all potential risks and problems that could happen during production.
It is a 6-step approach to validating a BOM. This process is designed to ensure that the BOM is accurate and complete at all levels.
- Step 1
The first step in the process of validating a BOM is to identify the level. There are three levels of BOM which include Finished Products, Sub-Assemblies and Components. The higher the level, the more detailed and thorough the validation will
be. - Step 2
The second step in this process is to identify the type of BOM being validated. There are two types of BOMs that can be validated, which include Engineering Bills of Material (EBOM) and Manufacturing Bills of Material (MBOM). - Step 3
The third step is supplier engagement – collect, validate BOM data received from suppliers/manufacturers and standardize manufacturer name, part number, part description as per industry standard taxonomy, also eliminate duplicate parts. - Step 4
A detailed lifecycle analysis to ensure that the assemblies are designed based on the right components, help the procurement team to manage alternate sourcing and raise alarms for obsolescence. - Step 5
An accurate BOM will be generated in the form of an intuitive tree structure that helps roll the parts into subassemblies and increases supply chain efficiency. - Step 6
Integrate multiple systems to ensure the data is the same across functions, manufacturing sites and systems such as ERP, and EAM.
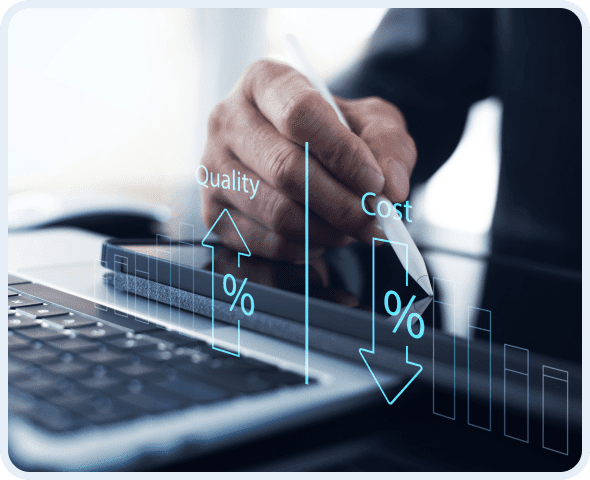
Benefits of BOM validation
- Production efficiency: Speeding up assembly time
- Quality assurance: Ensuring that the right parts are used in manufacturing
- Cost savings: Eliminating the high costs of procurement and obsolescence
Speak to one of our Component Engineering specialists today, and we will perform a detailed DFM (Design for Manufacturability) analysis of your current BOM services. In addition to saving time and money, we will eliminate the stress of sourcing and finding the correct components, which will also help you with strategic production planning.